Lubrication Of Rotary Drying Kiln
Why Lubricate the Riding-ring Tracks?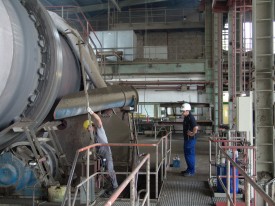
Due to the heat radiation, rotary drying kilns are supported by a riding-ring. The riding-ring and the kiln drum have different operating temperatures. Both components must be able to compensate for thermal expansion.
For this reason, the riding-ring and the kiln drum are matched with a loose tolerance. Slide plates are often located between the kiln shell and the ring. Insufficient lubrication causes excessive force (due to relative movement) to be excerted on the bearing support of the ring. This may lead to a deformation of the kiln shell. Manufacturers prescribe daily lubrication; depending on the tolerance, 1 - 3 cu. cm of special emulsion should be applied.
Conventional systems use hand-spray devices with a lance to apply the lubricant. Such systems often use a pressure vessel to apply the lubricant, thereby requiring maintence personnel to squeeze between the gaps whilst on a ladder and being subjected to the heat of the kiln. The rotary motion of the kiln often leads to a feeling of dizziness which increases the risk of accident. This method of results in non-lubricated spots or leads to under- or over-lubrication.

Advantages of Automated Riding Ring Lubrication
A fully-automated lubrication system enables precise and metered spraying of lubricant to the contact area. A lazer sensor counts the gaps and controls the spray impulses. The number of cycles is adjusted, and a distance of up to 1 mtr can be accommodated between spray nozzle and the point of lubrication.
Function
A central lubrication pump fills an external accumulator via a main supply line. A pressure switch mounted on the accumulator generates a "primary" pressure of around 90 bar and a filling pressure of 60 bar. The accumulator ensures that lubricant is available during operating times.
The lubricant delivery is initiated by a lazer sensor that signals the solenoid valve to open, allowing lubricant to be spray-applied into the voids of the rolling race, via the spray nozzles. After a pre-determined number of cycles, adjustable via the controller, the pause time begins and the system pressure is dissipated via a 2/2-way solenoid valve at the pump.
System Benefits
- Fully-automated system
- Precise and metered spraying of slide plates
- Spray distance of up to 1 mtr
- A lazer sensor counts the voids and signals the spray impulse
- The number of cycles is adjustable
- Complete pre-assembled pump station with controller (plug and play)
|